summary: the pier itself can be made out of metal anchored on a concrete slab, concrete tube or cinder blocks.
The mount plate is then anchored in the pier.
The mount is bolted to the mount plate.
The mount plate
The mount plate can be done by re-purposing a brake rotor as seen here $10
The base of the fork mount is about 9" in diameter and has 2 sets of 3 holes. The innermost set is about 3" from center, the set we're interested in is the outtermost which are 80mm from the center.
The screws are 3/8" x 16 tpi (ref. @mclewis1)
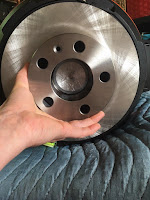
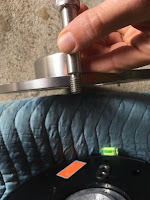
2020-06-20: Upgrading to a telescoping pier. Based on Davey-T design.
Outer tube: square tube 6", I'll angle grind the brake to fit inside the 6" tube then tap 4 holes at 3/8" x 16tpiInner tube: 4 x iron angles welded together. Could be replaced by a 5" square tube if the linear actuator can fit and not be a pain to weld in place. Here is an idea: weld the linear actuator to a base then weld the base inside the 5", problem is how do I remove it when the LA fails? idea: weld the lower angle that the LA is attached to to a tapped piece of metal then bolt that piece of metal to the 5"
In-between: 5mm PTFE sheets
Motor: Linear actuator
Details: Two bolts to tighten things up after movement.
FCAW Welder:
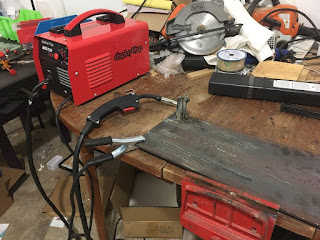
Back from the metal scrapyard with scrap, now training the welding.
I can still smell the flux hours later, that can't be good. Flushed water through my nostril made it go away. The next day wore masks and now I no longer smell metal in my nose.
For the inner tube Davey uses 4 iron angles. This is a good alternative to the central tube because it reduces the space between inner and outer tube and also makes mounting and replacing the linear actuator easier as there is space to nudge it. A shorter 5" central tube is cut in half and iron angles are welded to it - or bolted from the inside, the iron angles need to be tapped. Space is reduced from over 8mm to 2mm which is easier to find PTFE for.